I realize it has been a while since the last update. Now that the cold weather is here I find myself ready to put the car on the lift for storage the rest of the year.
Some miles were added this year. Mostly short trips in known areas due to the excessively low oil sump height. This is on the list to get fixed in the off season.
Ultimately the car has a good summer season. It makes a fortune of power and was enjoyable to drive. One major issue has been the throttle hanging at mid throttle. Thankfully the brakes are up to the task. I did take the throttle body apart and polished it with 3000 grit sandpaper. It feels significantly smoother but we will find out next year.
First drive with the new power plant
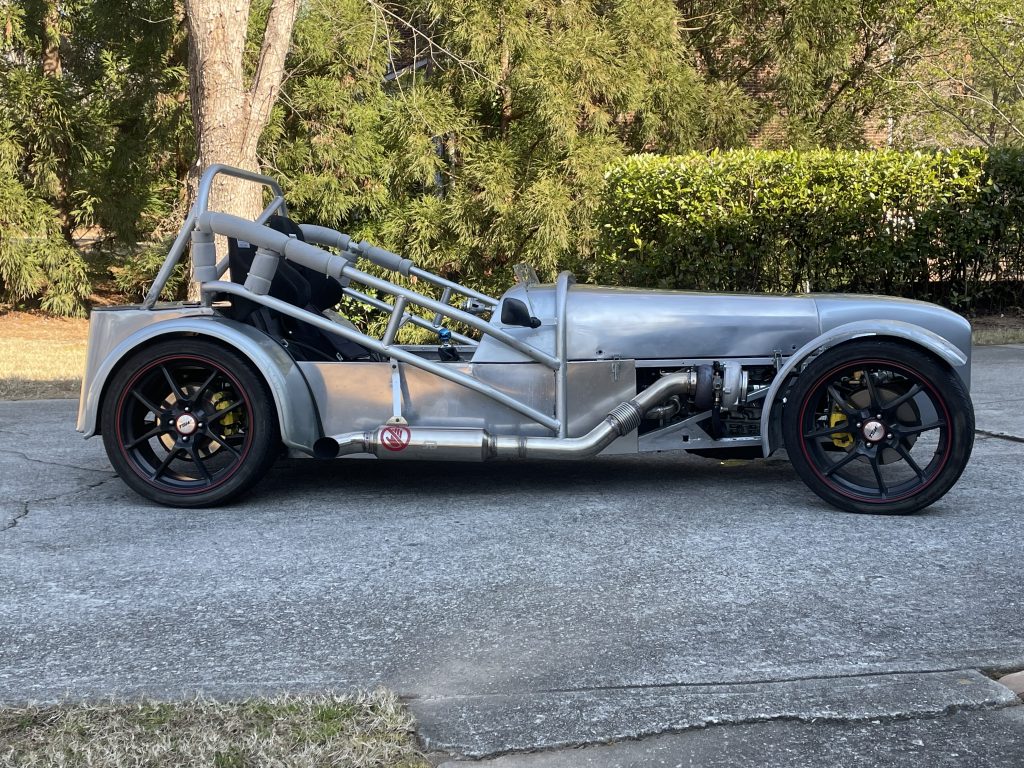
The perfect cold morning was the opportunity needed to put some road miles on the vehicle. With the sun shining I left the driveway and the vehicle was perfect! Engine hummed nicely. The turbocharger sung happily and the blow off valve worked for the first time since finding the vacuum leak.
Power delivery was smooth and driving around at low speed felt very comfortable. Upon hitting the gas the vehicle would unleash an army of houses and instantly cause the tire to summit and smoke to peel off their edges.
The only downside was a leaking 3 cent o-ring. Easy enough to fix and a fantastic day -even if only covering 49 miles!
Hitting the dyno
The day finally came that I could get the car on the rollers. I’m very thankful to have some fantastic friends that helped me get to this point as well as beyond. My buddy Neil let me borrow his trailer (perfect 7 size!) and Dave that owns Complete Performance has been a friend for years.
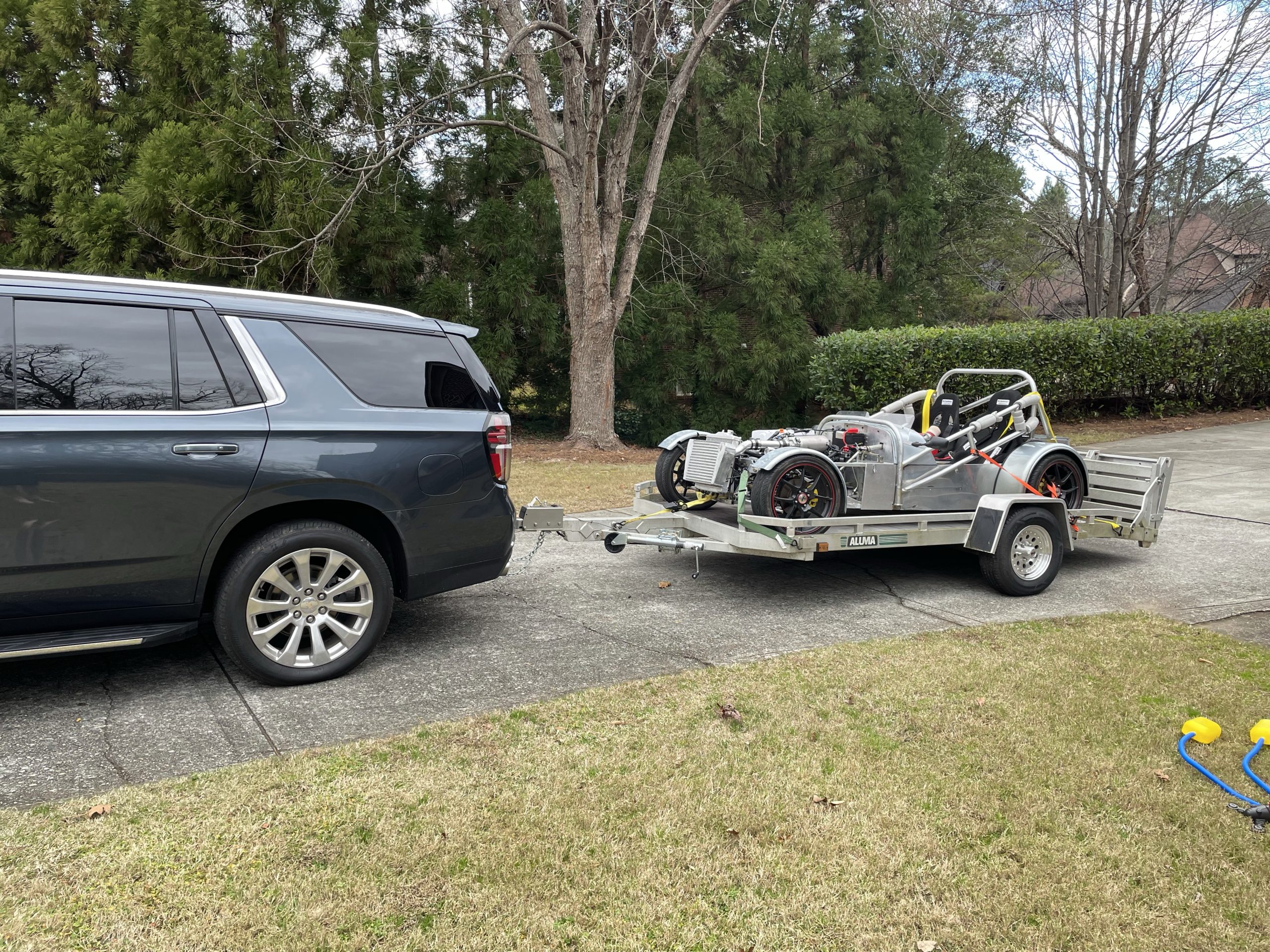
Car fits perfectly on the trailer Neil uses for his radical.
Admittedly the car wasn’t behaving when it went on the trailer. My attempt to change base fuel pressure was not perfect and resulted in a very soaked set of plugs.
Thankfully Dave has been around these issues and quickly helped diagnose the problem and a new set of plugs got us going again at 43.5psi of fuel pressure. Up next was to do some basic pulls to 4000rpm. Our goal was to check that everything worked together and we didn’t have surprises.
Like with any car that has not been tested we found a few bugs. The first was an issue in which we made 12psi of boost-twice what the watergate spring was supposed to make. Dave quickly found the push lock line I used was too close to the turbo and has melted into the heat sleeve. Effectively we had no watergate connection and the tune would have gone to the moon.
The next problem was a water leak. The one thermostat housing has a connector that was an ORB connection. Unfortunately it’s poorly machined and it spits the o ring out. As a result we had a leak. The AN wrench helped us get it tight enough and not leaking. I will be replacing this soon (and probably adding Hondabond).
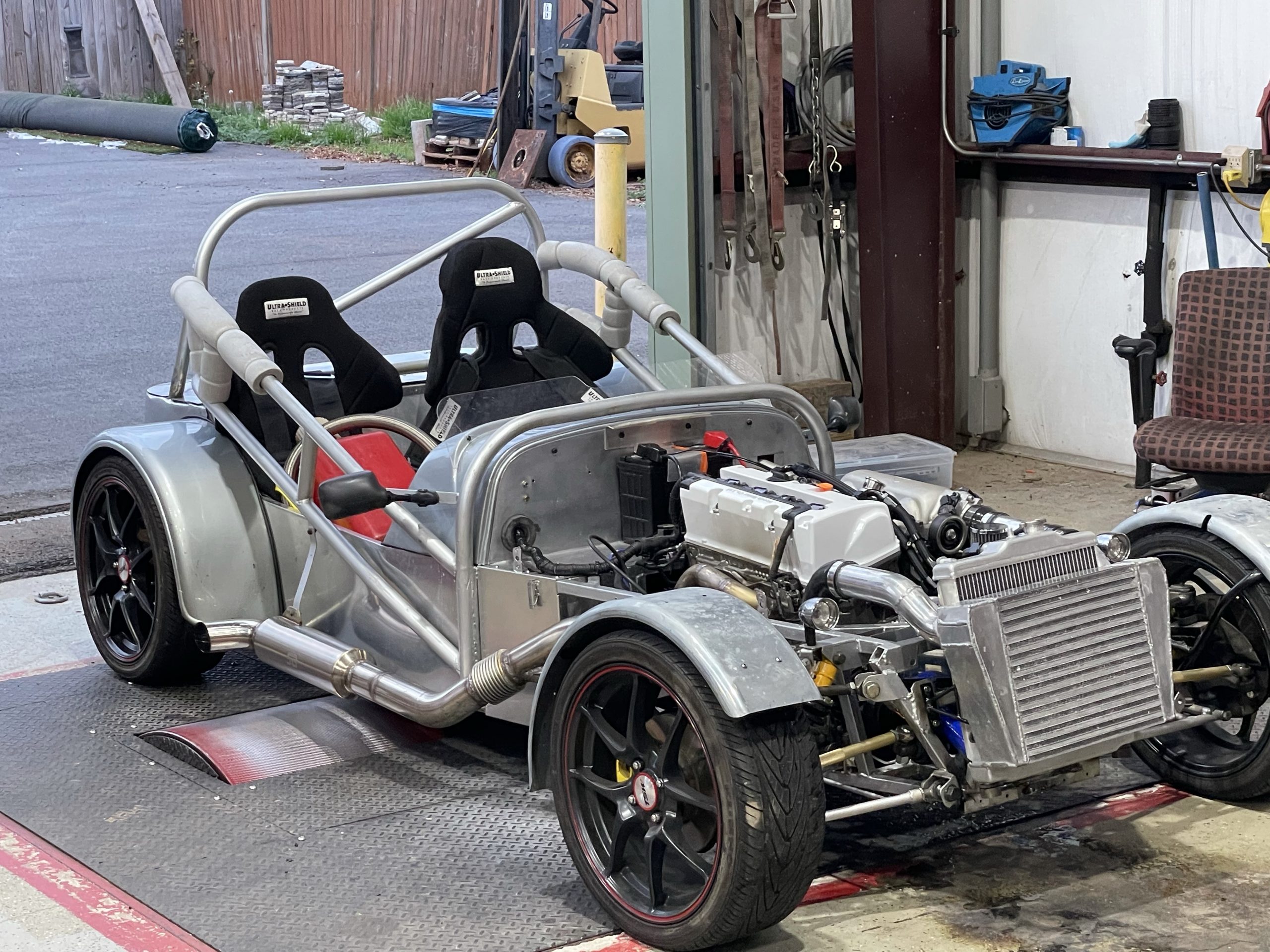
The next issue is one we haven’t fully understood but after a pull when the clutch is pushed in a spark would appear. I suspect the throw out bearing is not enjoying its kissing the pressure plate at 8500rpm
Ultimately we struggled to get the Hondata ecu to add and remove fuel as expected. Additionally learning in this area will be needed. A vtec code also emerged and you could heard a noise at the vtec cut over.
All in all a good day and I’m appreciative of the help and where it got me.
Video link is here –
https://youtu.be/InbHv2kdRBY
Too much fuel
The initial fuel injector purchase seems to have been a bad decision. The first set of injectors were 2000cc and turned out to be just a bit too big for pump gas.
The pulse width for idle on 93 octane was .02% and there was a heightened smell of informed fuel coming from the exhaust.
Why did I ever buy such large injectors? My goal is/was 650hp and e85 was the logical means to that goal. Unfortunately the availability isn’t great locally and from what I’ve seen it isn’t a great choice for cars not driven frequently. As a result I’ve lowered power expectations and only plan to use pump gas.
Replacement injectors were ordered. 1000cc injectors which I believe will provide enough power. The ability to turn up fuel pressure and potentially fuel pump voltage might be the answer.
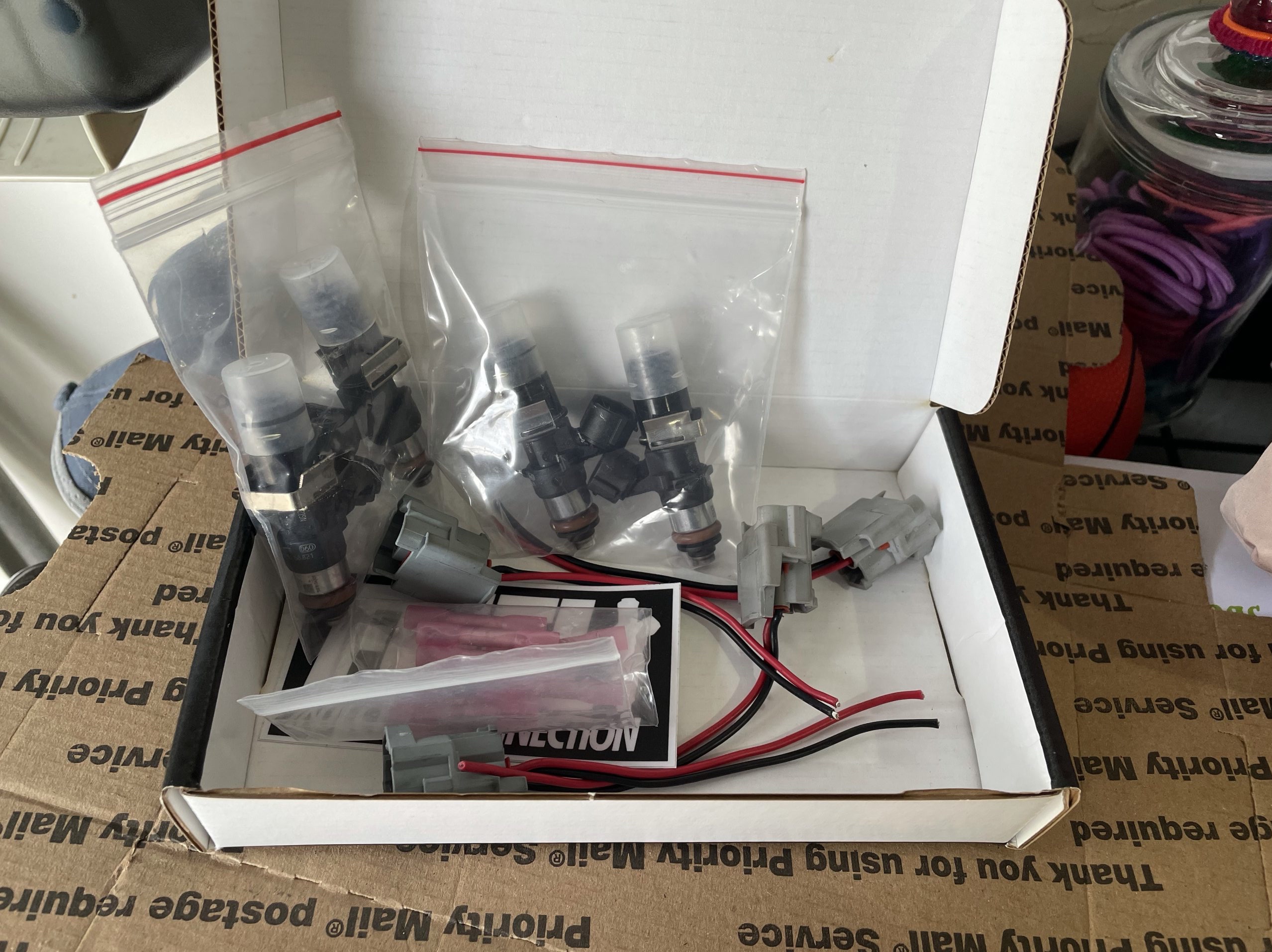
TPS problems…but solution!
The car starts SMS revs perfectly but a nagging problem is I would not see any indications on the software of a TPS signal below WOT. The problem produced odd behavior but I believed it was just how the Hondata ecu worked.
After driving and not seeing the tuning results in the data log I decided to pull the tps and flip it 180 degrees. I’m doing so I noticed the connection point was incorrect and the sensor was not making contact with the throttle shaft until 25% of the sweep happened. A small correction and things were showing TPS motion the entire way through the range. Timing is more responsive and drivability is better.
One problem remains. Under WOT I am not seeing boost over 1 psi. The watergate has a 7 psi spring in it and so something isn’t kosher. The hunt continues…
Cooling problems…
It took a while to resolve but finally everything is 99% done. The coolant problem was most likely caused by a bad (and brand new) thermostat. After adding aircraft piping with stainless heat jacket (see picture) we had some success but a small leak caused by npt and straight thread being incomparable. Eventually I changed to -16an and things are working fine.
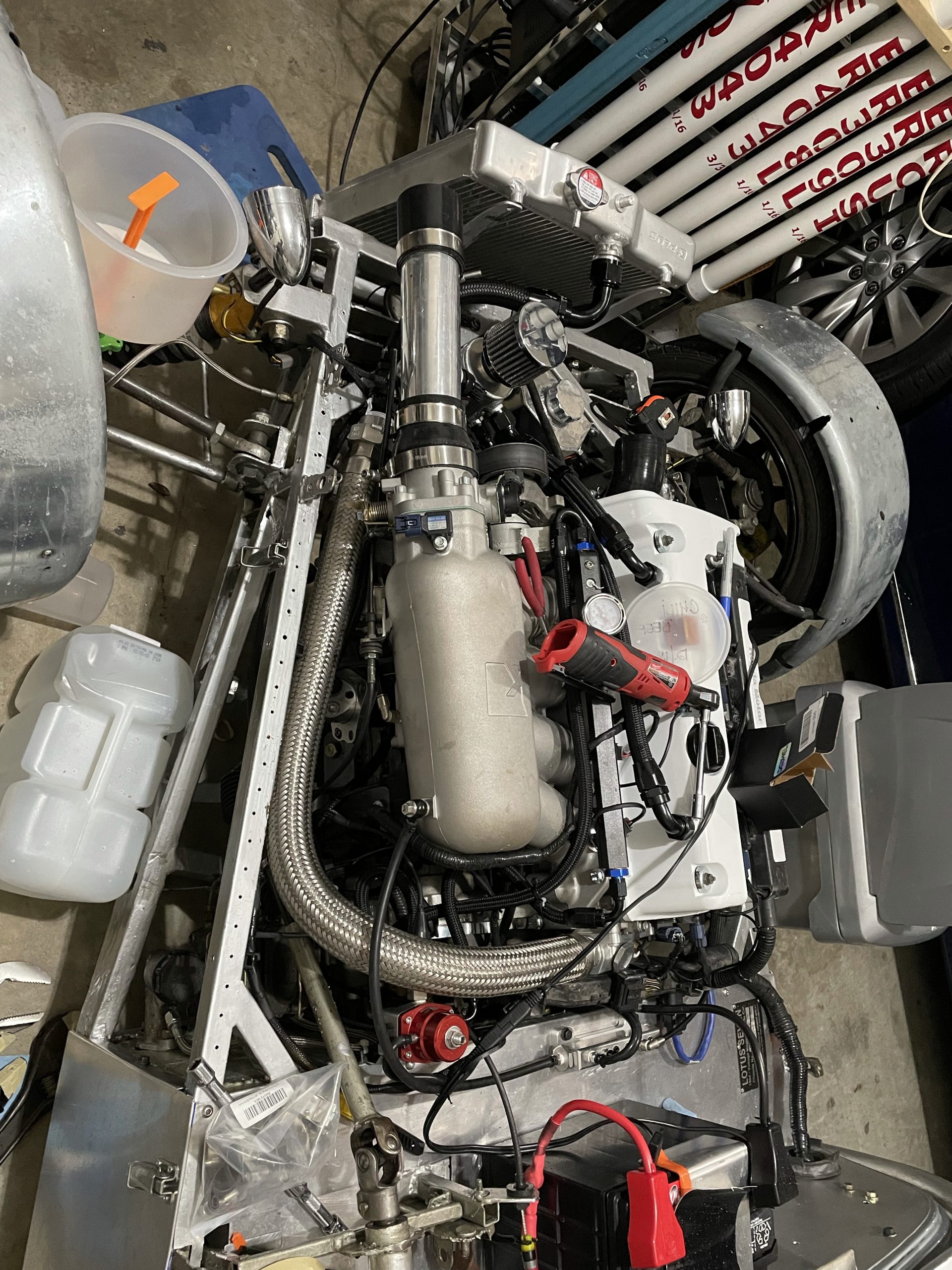
The radiator was replaced and -16 fittings welded on. There was a need for a shaped flexible coupler and so the piece below solved the problem.
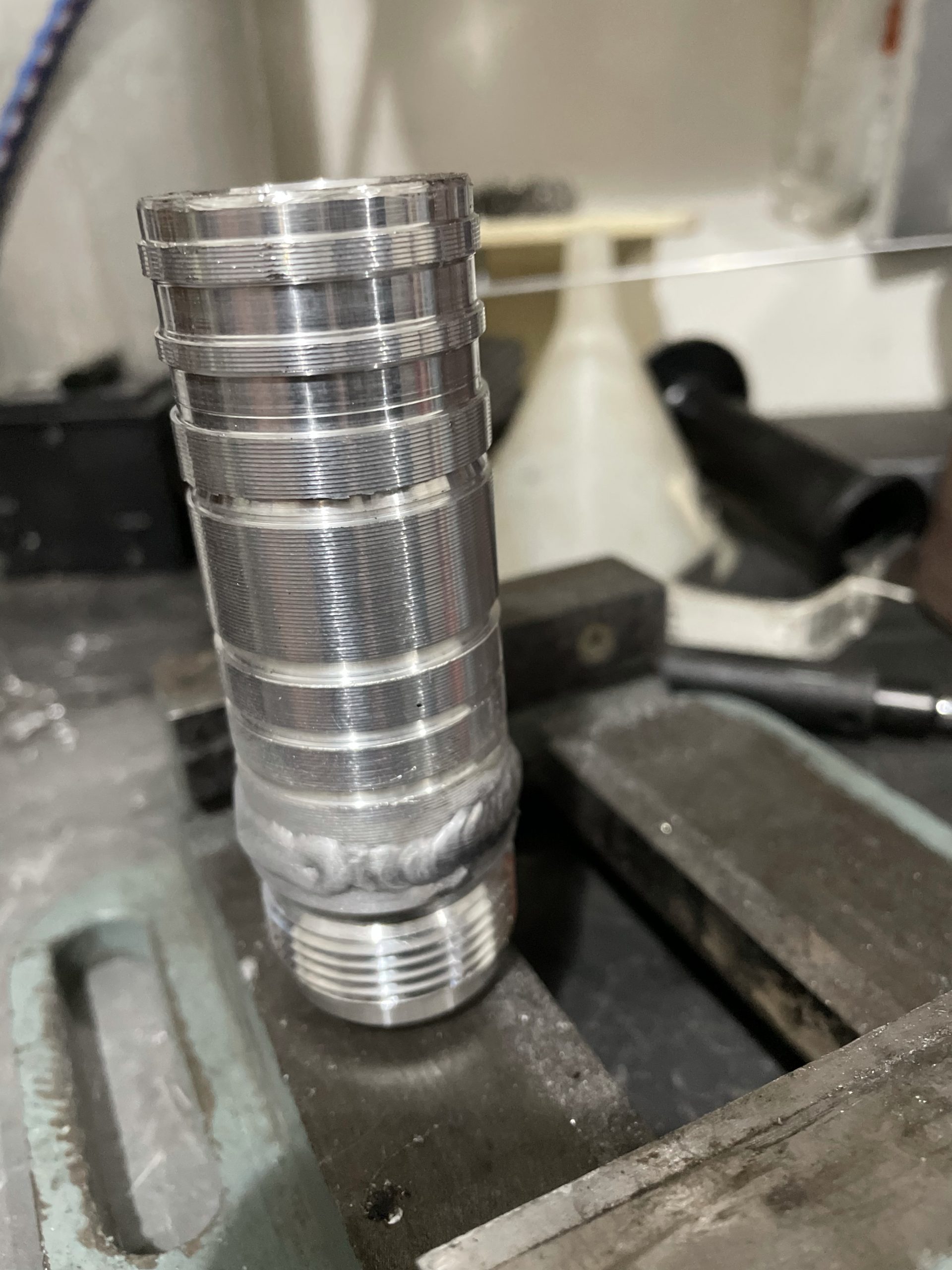
At this point things are lined up and ready to head to the tuner. Hopefully we get there one day soon. The car has 25 “neighborhood” miles on it and feels good. Still only 4 forward gears but fine for now.
So whats been happening?
Well unfortunately some international folks felt that hacking this page would really change the world.. or their world. I will try to upload some of the old content but backups apparently were not good.
Some people just suck…
Now steering in the right direction!
Adding the throttle body recently kick-started the progress of getting this thing back together but it also exposed a problem. The old steering shafts was pointed right where the alternator needed to live. I looked at several other alternator options but at the end of the day it made more sense to move the steering shafts than buy a different throttle body and find a way to make the alternator work.
Here was the old setup. The alternator lives right behind it.
The solution was actually easier than I expected. Woodward- the makers of the steering rack- had a variety of universal joints available and on the shelf. Some money was given to them and in return some shiny pieces arrived a few days later.
What is the plan? I expected to use 2 new universal joints to allow for some movement downwards and away from the engine. The results look promising and I manage to maintain my collapsible steering column setup!
Up next- transmission mounts!
Slow progress..but still progress!
It’s been slow and I have been looking to rent some space to use at night to further development of the car and get it ready before 2020.
After the engine was installed I decided I need to mock up drive belts and systems and get the steering sorted out. The next piece of the pie is the exhaust. Having built a header for U bends before I decided that I would like to avoid that again. The solution- a turbo manifold!
The hunt for a turbo was no simple task. Learning about mappings and what characteristics are important took up several hours in the evenings.
I decided on a Garrett G25-660 turbo. After lots of research I was price shopping and about to pull the trigger and an eBay price alert went off. Long story short- I was able to get a GT3076R dual ball bearing unit for $700 that was new in the box. It won’t have the same low end but it should fine given the ball bearings.
Next step is to order a kit to build the rams horn turbo manifold!
K20 Power now bolted in!
It took a while but I snuck a half day into working on the car with my dad. While I thought it was 3 hours of work it actually took 6.
First thing was to pull the k20a3 and remove the transmission and adapter plate.
Up next was moving those parts to the K20z3 and bolting them all back together.
From there we worked out what needed to be changed and we we removed and replaced a tube in the chassis. We also removed the old motor mounting plate and cut a new piece. After 5-10 minutes of welding we started to position the engine.
After measuring and cutting several tubes we had the left side mounted. Next we leveled the engine to 0.6 degrees and started on the driver side. They came out quite well
The final step was to check hood clearance. I didn’t expect it to fit but was nicely surprised. 3 mm to spare!
There week be some challenges with the steering and alternator but those are for a different day!
Ground clearance is a nice and acceptable 4″
Up next is the transmission mounts!