The day finally came that I could get the car on the rollers. I’m very thankful to have some fantastic friends that helped me get to this point as well as beyond. My buddy Neil let me borrow his trailer (perfect 7 size!) and Dave that owns Complete Performance has been a friend for years.
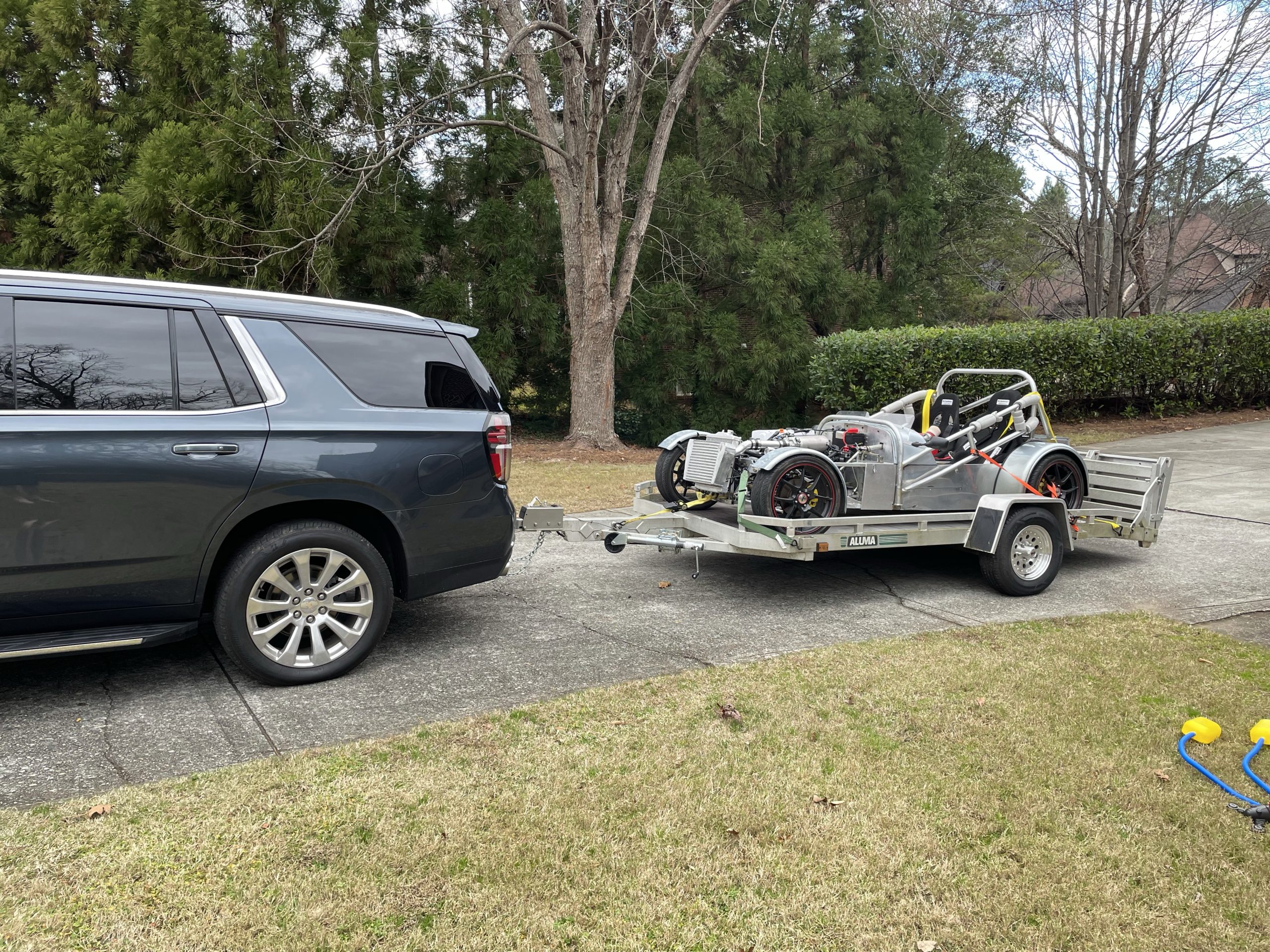
Car fits perfectly on the trailer Neil uses for his radical.
Admittedly the car wasn’t behaving when it went on the trailer. My attempt to change base fuel pressure was not perfect and resulted in a very soaked set of plugs.
Thankfully Dave has been around these issues and quickly helped diagnose the problem and a new set of plugs got us going again at 43.5psi of fuel pressure. Up next was to do some basic pulls to 4000rpm. Our goal was to check that everything worked together and we didn’t have surprises.
Like with any car that has not been tested we found a few bugs. The first was an issue in which we made 12psi of boost-twice what the watergate spring was supposed to make. Dave quickly found the push lock line I used was too close to the turbo and has melted into the heat sleeve. Effectively we had no watergate connection and the tune would have gone to the moon.
The next problem was a water leak. The one thermostat housing has a connector that was an ORB connection. Unfortunately it’s poorly machined and it spits the o ring out. As a result we had a leak. The AN wrench helped us get it tight enough and not leaking. I will be replacing this soon (and probably adding Hondabond).
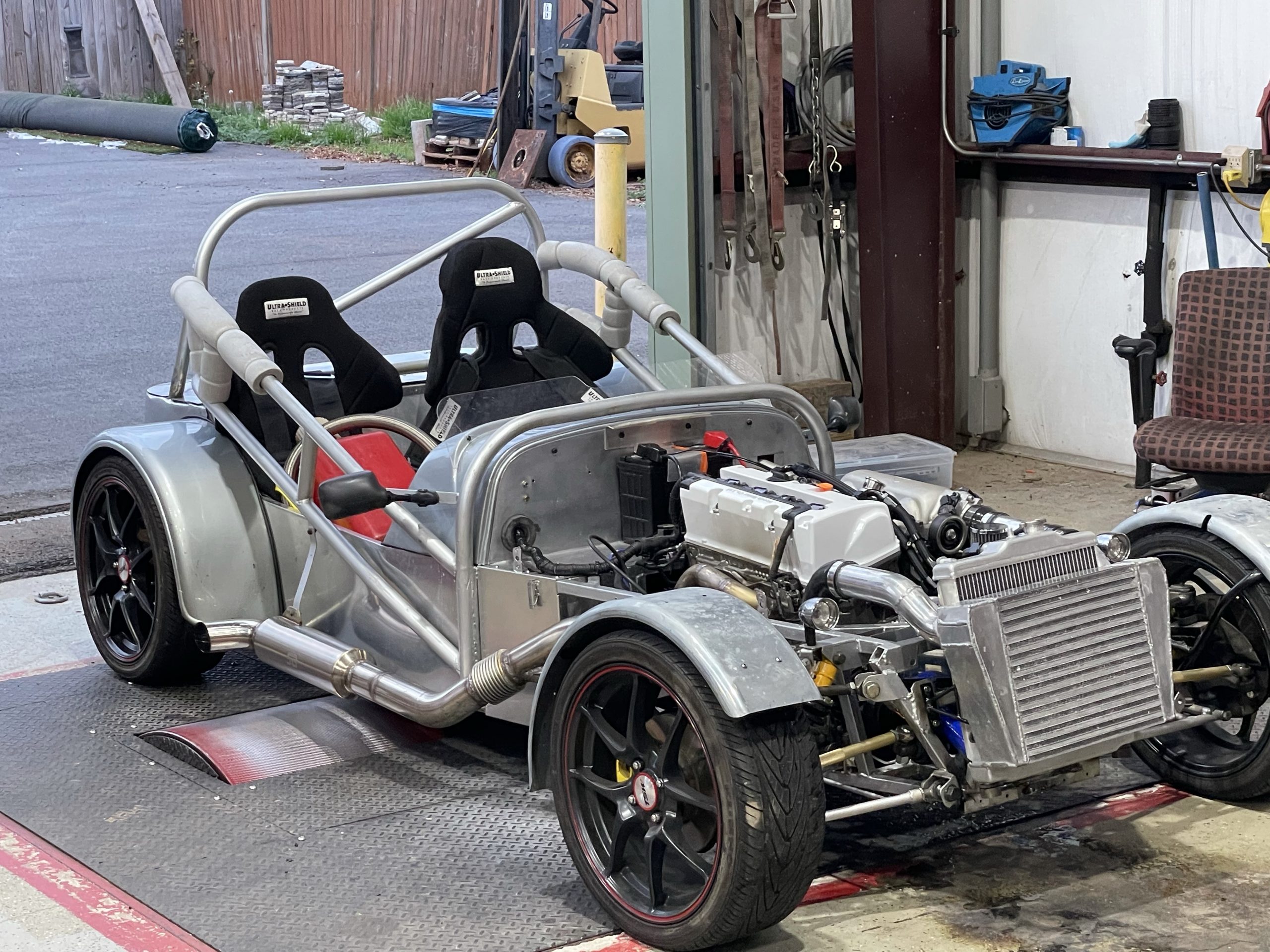
The next issue is one we haven’t fully understood but after a pull when the clutch is pushed in a spark would appear. I suspect the throw out bearing is not enjoying its kissing the pressure plate at 8500rpm
Ultimately we struggled to get the Hondata ecu to add and remove fuel as expected. Additionally learning in this area will be needed. A vtec code also emerged and you could heard a noise at the vtec cut over.
All in all a good day and I’m appreciative of the help and where it got me.
Video link is here –
https://youtu.be/InbHv2kdRBY